compound granule for plastic container
A compound granule for plastic container refers to a pre-formulated blend of polymer resins, additives, stabilizers, colorants, and sometimes fillers, designed for specific properties and manufacturing requirements. These granules are the raw material used in processes like injection molding, blow molding, or extrusion to produce plastic containers.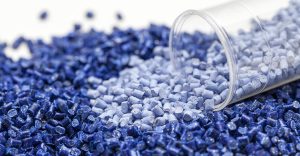
Composition of Compound Granules
- Base Polymer (Resin):
- The primary material, providing the structural and functional properties of the container. Examples:
- HDPE for rigid, chemical-resistant containers.
- PP for heat-resistant and lightweight containers.
- PET for clear and tough containers.
- Additives:
- Modify or enhance the properties of the polymer for specific applications.
- Common additives include:
- Colorants: Create the desired color (e.g., pigments or masterbatches).
- UV Stabilizers: Protect the material from degrading under sunlight.
- Impact Modifiers: Improve the toughness and prevent cracking.
- Plasticizers: Enhance flexibility (used mainly in PVC).
- Antioxidants: Prevent the polymer from oxidizing during processing or use.
- Anti-slip or Anti-block Agents: Prevent surfaces from sticking together.
- Fillers:
- Materials like calcium carbonate or talc may be added to reduce costs or improve stiffness, weight, or thermal properties.
- Barrier Materials (Optional):
- For containers that need to block gases or moisture, such as food and beverage packaging, special materials like EVOH (ethylene vinyl alcohol) are included.
Manufacturing Process of Granules
- Mixing:
- The base resin is mixed with the required additives in specific proportions.
- Compounding:
- The mixture is heated and blended in an extruder to achieve uniform distribution of all components.
- Granulation:
- The molten polymer is cooled and chopped into granules or pellets, making it easy to handle and use.
Key Properties for Plastic Containers
Plastic containers must meet various criteria depending on their end use. Here are some key properties granules can be engineered to achieve:
- Mechanical Strength:
- To withstand impact, pressure, and loads.
- For example, HDPE granules are used for strong industrial containers.
- Chemical Resistance:
- Essential for storing chemicals or cleaning agents.
- PP or HDPE is commonly chosen for these applications.
- Transparency and Aesthetics:
- For products like PET beverage bottles or cosmetic containers.
- Special additives ensure clarity and gloss.
- Barrier Properties:
- To prevent gas, moisture, or odor permeation, critical for food containers.
- Food Safety Compliance:
- For food and beverage containers, the materials must comply with FDA, EU, or other regulatory standards. No toxic substances like heavy metals or BPA (in some regions) are allowed.
- Environmental Considerations:
- Increasing demand for bioplastics or recyclable plastics to reduce environmental impact.
Common Processing Methods for Plastic Containers
- Injection Molding:
- Used for creating rigid containers and lids by injecting molten granules into a mold.
- Blow Molding:
- Used for hollow containers like bottles. There are two main types:
- Extrusion Blow Molding: For simpler shapes like milk jugs.
- Injection Blow Molding: For more intricate shapes and better surface finishes.
- Extrusion:
- Used for producing plastic sheets or films for thermoforming containers.
- Thermoforming:
- Heated sheets of plastic are formed into container shapes, often used for disposable food trays and lids.
Customization for Different Applications
- Food and Beverage:
- Use PET, PP, or HDPE for safety and clarity. These granules often have antimicrobial additives or are co-extruded with barrier layers.
- Pharmaceuticals and Cosmetics:
- PP or HDPE granules are chosen for chemical resistance and tamper-proof sealing.
- Industrial and Chemical Use:
- Containers for cleaning agents or industrial chemicals use highly durable and chemical-resistant granules like HDPE.
- Eco-Friendly Options:
- Granules made of bioplastics (e.g., PLA) or recycled content are increasingly used for sustainable packaging.
Advantages of Using Compound Granules
- Consistency:
- Uniform material properties ensure predictable performance during processing and in final products.
- Customizability:
- Tailored to specific needs like impact resistance, transparency, or lightweighting.
- Ease of Processing:
- Granules flow smoothly in machines, reducing downtime and waste.
- Cost Efficiency:
- Optimized formulations can reduce material and production costs while maintaining quality.
AMTOP.CO
hdpe granule for injection is not just a trend but a necessary step toward reducing plastic pollution and achieving sustainability in manufacturing. By overcoming challenges and leveraging technological advances, manufacturers can unlock its full potential in a variety of applications.