Recycled hdpe for injection
Recycled hdpe for injection is a comprehensive process that involves transforming used plastic into usable raw materials for creating new products. Here’s an in-depth explanation of each step and consideration: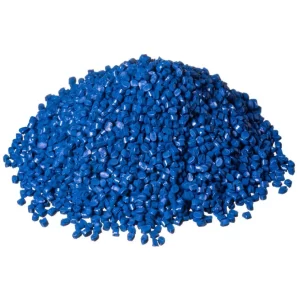
Collection and Sorting
- Sources of Recycled HDPE:
- Post-consumer HDPE: These include discarded items like milk jugs, shampoo bottles, and detergent containers. They form a significant portion of recycled HDPE.
- Post-industrial HDPE: This comes from manufacturing scrap such as trimmings or unused parts, which are often clean and easier to recycle.
- Sorting Methods:
Advanced sorting technologies like infrared scanners, density separation (sink-float method), and manual sorting are used to separate HDPE from other plastics (e.g., PET, LDPE) and contaminants like metals or paper.
Cleaning
- Cleaning is essential to ensure the recycled HDPE is free from contamination, which can degrade the quality of the final product.
- Steps in Cleaning:
- Pre-washing: Removal of dirt, food residues, and loose contaminants.
- Label and Adhesive Removal: Mechanical or chemical treatments strip labels and adhesives that could clog machines or affect the quality of the plastic.
- Drying: Proper drying prevents moisture from causing problems like bubbles or weak spots in the molded parts.
Shredding and Pelletizing
Once cleaned, the HDPE is prepared for use in injection molding.
- Shredding:
Large pieces of HDPE are shredded into small flakes to facilitate uniform melting.
- Pelletizing:
The flakes are melted, filtered to remove contaminants, and extruded into pellets. This step ensures:
- Uniform size and shape for consistent feeding into molding machines.
- Improved quality control by allowing precise blending with additives or virgin HDPE.
Additives and Blending
Recycled HDPE may need enhancements to meet specific requirements for injection molding.
- Common Additives:
- UV Stabilizers: Protect against sunlight degradation in outdoor products.
- Impact Modifiers: Improve toughness for applications like automotive parts.
- Colorants: Add or adjust color, often to mask inconsistencies in recycled material.
- Blending with Virgin HDPE:
Recycled HDPE can be mixed with virgin material to achieve desired properties (e.g., strength, flexibility, or heat resistance) while maintaining a lower cost and environmental benefit.

Injection Molding with Recycled HDPE
The injection molding process involves several stages, optimized for the properties of recycled HDPE:
Feeding and Melting
- Recycled HDPE pellets are fed into the hopper of an injection molding machine.
- Inside the machine, a screw rotates and pushes the material into a heated barrel where it melts.
Injection and Cooling
- The molten plastic is injected under high pressure into a mold, which shapes the part.
- Cooling solidifies the material, locking it into the desired form.
Ejection
- Once cooled, the molded part is ejected from the mold. Post-processing (e.g., trimming, polishing) may be performed to remove imperfections.
Applications of Recycled HDPE
Recycled HDPE is used in a variety of industries:
- Industrial Applications:
- Piping and Conduits: Resistant to chemicals and corrosion.
- Shipping Pallets and Crates: Durable and load-bearing.
- Consumer Products:
- Household Goods: Buckets, bins, and containers.
- Outdoor Furniture: Resistant to weather and UV light.
- Automotive Parts:
- Under-hood components and protective covers.
- Agricultural Products:
- Irrigation tubing and storage tanks.
Benefits of Using Recycled HDPE
- Environmental Impact:
- Diverts plastic waste from landfills and oceans.
- Reduces dependence on fossil fuels needed for virgin plastic production.
- Lowers carbon footprint by requiring less energy than creating virgin HDPE.
- Cost Savings:
Recycled HDPE is often cheaper than virgin material, reducing manufacturing costs.
- Sustainability:
Brands using recycled HDPE can market products as eco-friendly, aligning with consumer demand for sustainable practices.
Challenges in Using Recycled HDPE
- Material Variability:
The quality of recycled HDPE depends on the source material and processing. Contaminants or mixed plastics can affect performance.
- Processing Difficulties:
- Moisture: Residual water can create bubbles or weak points.
- Degradation: Multiple recycling cycles may reduce polymer strength.
- Regulatory Compliance:
Meeting health and safety standards for food-grade or medical applications can be challenging. Proper sorting and certification are required.
Quality Assurance and Testing
To ensure consistent quality, recycled HDPE undergoes rigorous testing:
- Melt Flow Index (MFI): Measures how easily the material flows during molding.
- Tensile Strength: Ensures durability for its intended application.
- Chemical Resistance: Verifies the material’s ability to withstand various substances.
Innovations in Recycled HDPE
- Advanced Recycling Technologies:
Chemical recycling processes break HDPE down to its monomers for nearly virgin-quality material.
- Improved Sorting Systems:
AI and robotics are enhancing the efficiency and accuracy of separating HDPE from waste streams.
- Bio-enhanced HDPE:
Some manufacturers incorporate bio-based feedstocks with recycled HDPE for hybrid solutions.
AMTOP.CO
Recycled HDPE for injection molding is not just a trend but a necessary step toward reducing plastic pollution and achieving sustainability in manufacturing. By overcoming challenges and leveraging technological advances, manufacturers can unlock its full potential in a variety of applications.