PE GRANULES FOR FILM
PE GRANULES FOR FILM, especially LDPE, HDPE, and LLDPE, play a crucial role in producing films used for various applications, from everyday plastic bags to specialized industrial packaging. Here’s a more detailed explanation:
Understanding Polyethylene (PE):
Polyethylene is a thermoplastic polymer made from ethylene monomers. It is one of the most commonly used plastics due to its versatility, chemical resistance, and low cost of production. In its granule form, PE is melted and molded into various products, including plastic films, which are highly used in the packaging industry.
Types of Polyethylene for Film:
a. LDPE (Low-Density Polyethylene):
- Properties:
- Low-density: LDPE has a more branched structure than other types of polyethylene, leading to lower density and more flexibility.
- Flexibility: It can stretch and bend without breaking, making it ideal for films that need to be flexible.
- Transparency: It has relatively good optical properties, meaning it produces films with decent clarity.
- Moisture Barrier: LDPE films offer moderate protection against moisture, making them suitable for packaging that requires moisture resistance.
- Applications of LDPE Film:
- Plastic bags: Shopping bags, food bags, and trash bags are typically made from LDPE film.
- Shrink wrap and stretch wrap: These films are used for wrapping pallets and products to protect them during transport.
- Agricultural films: LDPE is used for mulching films to retain moisture in the soil and protect crops.
- Lamination films: LDPE is also used as a layer in multi-layer films, providing flexibility and sealing properties.
b. HDPE (High-Density Polyethylene):
- Properties:
- High density: HDPE has a linear structure with less branching, leading to higher density and rigidity.
- Strength: HDPE films are more durable and stronger than LDPE films, with greater resistance to tearing and puncturing.
- Moisture resistance: HDPE films provide better protection against moisture than LDPE films.
- Opacity: HDPE films are less transparent than LDPE films, but they offer better strength and protection.
- Applications of HDPE Film:
- Industrial packaging: Heavy-duty bags and sacks used for storing bulk goods like fertilizers or chemicals are made from HDPE film.
- Grocery bags: HDPE is commonly used for making durable and cost-effective grocery bags.
- Tarpaulins: HDPE films are used for making protective coverings, like tarps, due to their strength and durability.
- Construction materials: It is used in applications like vapor barriers and geomembranes.
c. LLDPE (Linear Low-Density Polyethylene):
- Properties:
- Strength and flexibility: LLDPE is more flexible and has better tensile strength than LDPE, making it suitable for films that need to withstand stretching or puncturing.
- Impact resistance: LLDPE films are less prone to tearing or puncturing compared to both LDPE and HDPE.
- Blown film or cast film: LLDPE can be used in both processes, giving manufacturers flexibility in the production process.
- Applications of LLDPE Film:
- Stretch films: These films are used for wrapping products on pallets, ensuring they are secure during shipping. LLDPE’s high strength and flexibility make it ideal for this application.
- Heavy-duty packaging: LLDPE films are used in packaging materials that need to withstand tough conditions, like bags for transporting heavy goods.
- Agricultural films: LLDPE can be used for greenhouses and mulch films due to its superior mechanical properties.
- Liners: LLDPE is often used as liners in packaging to provide moisture resistance and puncture protection.
Film Manufacturing Processes:
The type of film and its final application depends not only on the type of polyethylene used but also on the manufacturing process. There are two primary processes for producing PE films:
a. Blown Film Extrusion Process:
This process involves melting the PE granules and extruding the molten material through a circular die to form a tube. Air is blown into the tube, inflating it into a thin film. The film is then cooled and wound onto rolls.
- Benefits of Blown Film:
- It produces strong and uniform films.
- It allows for films of various thicknesses.
- This process is suitable for making both LDPE and HDPE films.
- Common uses:
- Plastic bags
- Shrink wraps
- Agricultural films
b. Cast Film Extrusion Process:
In the cast film process, PE granules are melted and forced through a flat die, producing a sheet of film. The film is then cooled on a chilled roller and wound into rolls.
- Benefits of Cast Film:
- High clarity films due to the faster cooling.
- More precise control over film thickness and properties.
- Ideal for making multi-layer films (combining different properties in one film).
- Common uses:
- Cling films
- Barrier films (for food packaging)
- Lamination films
Additives and Modifications:
PE granules can be customized for specific applications by adding different additives during the manufacturing process. These additives help modify the physical and chemical properties of the PE films, such as:
- UV stabilizers: To prevent film degradation from sunlight, especially for agricultural films.
- Anti-static agents: To reduce static build-up in the film, often used in packaging for electronics.
- Slip agents: To reduce friction, making the films easier to handle and process.
- Colorants: To provide different color options for branding or product differentiation.
- Barrier properties: For films used in food packaging to extend shelf life by providing gas or moisture barriers.
Choosing the Right PE Granule for Film Production:
When selecting the right PE granule type, consider the following factors:
- Application requirements: Whether the film needs to be rigid, flexible, transparent, or opaque will determine the type of PE granule used.
- Strength and durability: For heavy-duty films or those exposed to harsh conditions, HDPE or LLDPE may be better suited due to their higher tensile strength.
- Clarity: If high transparency is a priority, LDPE or cast LLDPE films would be more suitable.
- Barrier properties: LDPE and HDPE offer moisture resistance, but additional layers or additives may be necessary for films requiring protection from gases or UV light.
Environmental Considerations:
PE films, especially single-use plastic films like bags and wraps, contribute to plastic waste. However, polyethylene is highly recyclable, and many film manufacturers are moving towards using recycled PE granules or developing bio-based PE films to reduce environmental impact.
- Recycled PE: Many manufacturers use recycled PE to produce films, reducing the environmental footprint of the products.
- Biodegradable films: Efforts are being made to produce biodegradable films using PE that break down more easily in the environment.
In summary, PE granules (LDPE, HDPE, and LLDPE) offer unique properties that can be tailored to the needs of various film applications. The choice of granule type, additives, and manufacturing process determines the performance and functionality of the final film product, whether for simple plastic bags or advanced packaging materials.
(FAQ)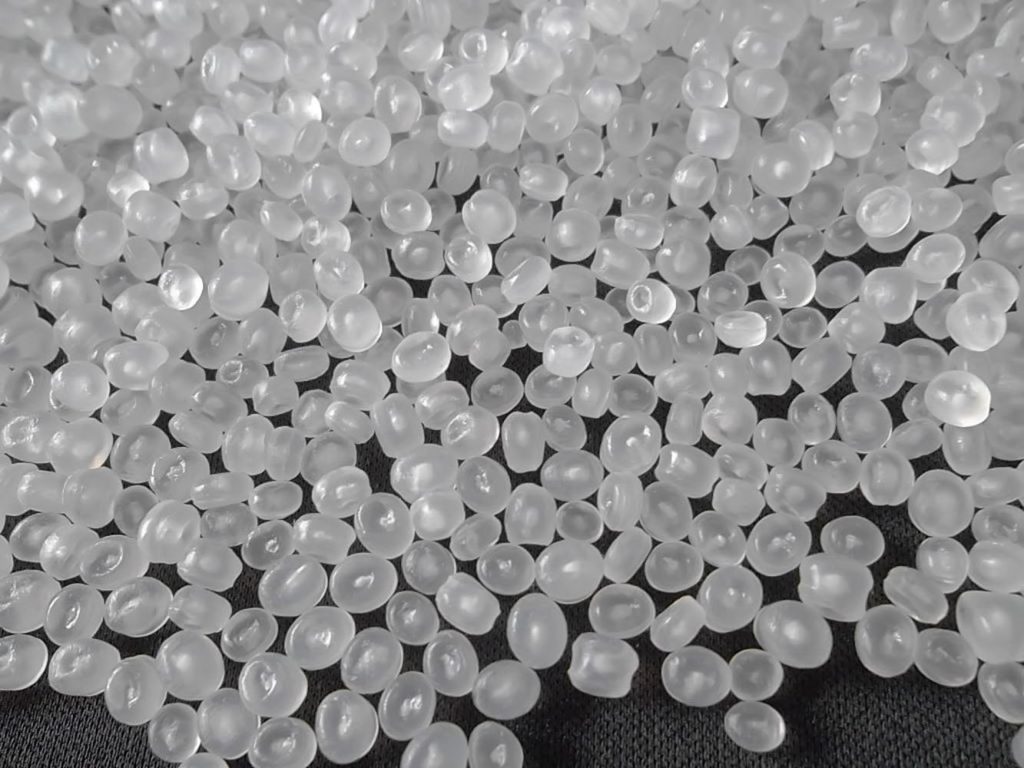
What are PE granules?
PE (Polyethylene) granules are small plastic pellets made from polyethylene resin. These granules are the raw material used in the production of various plastic products, including films, through processes like extrusion and molding.
What are the main types of polyethylene used for film production?
The three main types of polyethylene used for film production are:
- LDPE (Low-Density Polyethylene) – Known for flexibility and clarity.
- HDPE (High-Density Polyethylene) – Offers strength and rigidity.
- LLDPE (Linear Low-Density Polyethylene) – Provides higher tensile strength and impact resistance.
What is the difference between LDPE and HDPE in film production?
- LDPE: It is more flexible, offers better transparency, and is often used for stretch films, plastic bags, and packaging.
- HDPE: It is stiffer, stronger, and more opaque, often used for heavier-duty applications like industrial packaging and grocery bags.
What is LLDPE used for in film production?
LLDPE is primarily used for stretch films, agricultural films, and heavy-duty packaging. It offers higher tensile strength and impact resistance compared to LDPE while maintaining flexibility.
What is the blown film extrusion process?
Blown film extrusion is a process where melted PE granules are extruded through a circular die and inflated into a tube shape by blowing air inside. This produces a thin film that is wound into rolls after cooling. It is commonly used to produce plastic bags, packaging films, and agricultural films.
What is cast film extrusion?
In the cast film extrusion process, molten PE granules are forced through a flat die to form a continuous sheet of film. The film is cooled by passing over a chilled roller, producing high-clarity films with precise thickness control. This process is typically used for producing cling films and lamination films.
Can PE granules be recycled?
Yes, polyethylene is recyclable, and many PE films can be made from recycled PE granules. Recycling PE helps reduce plastic waste and the environmental impact of single-use plastic films.