LDPE granule for extrusion film
LDPE (Low-Density Polyethylene) granules are popular in film extrusion due to their balance of flexibility, strength, and ease of processing. Let’s delve deeper into why LDPE is chosen for film extrusion, how it’s processed, and what makes it suitable for a variety of film applications.
Why LDPE is Ideal for Film Extrusion
LDPE is characterized by its unique molecular structure, where the chains are highly branched. This branching prevents the polymer chains from packing closely together, giving LDPE its lower density compared to high-density polyethylene (HDPE). This structure is responsible for LDPE’s main properties:
- High Flexibility and Softness: LDPE’s molecular structure results in a material that is both flexible and resilient. This flexibility makes it ideal for films that need to bend or stretch without breaking, such as plastic bags or shrink wraps.
- Transparency: LDPE films are often clear, which is ideal for packaging applications where product visibility is important. The level of transparency can be controlled by adjusting the thickness and additives.
- Sealability: LDPE has excellent heat-sealing properties, which is crucial for applications like food packaging or liners where a tight seal is needed to protect contents from contaminants or air.
- Resistance to Chemicals and Moisture: LDPE’s non-polar structure provides strong resistance against moisture and many chemicals, ensuring that the film protects the products it encases. This makes LDPE suitable for agricultural films and packaging materials that require durability against environmental exposure.
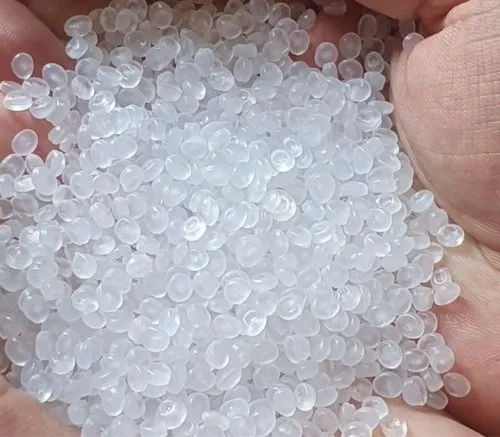
Key Properties of LDPE granule for extrusion film
Before selecting LDPE granules, it’s essential to understand key properties that influence the quality and functionality of the final film:
- Density (0.910 – 0.940 g/cm³): LDPE’s density is lower compared to HDPE. This lower density contributes to the material’s flexibility and transparency, which is beneficial for producing thin, clear films.
- Melt Flow Index (MFI): MFI, measured in grams per 10 minutes, indicates how easily the melted polymer can flow. For LDPE films, the typical MFI range is 0.2 to 20 g/10 min. Lower MFI values produce thicker, tougher films, while higher MFI values result in thinner films that flow more easily. Choosing the right MFI is essential to match the film thickness and processing speed required.
- Tensile Strength: LDPE has moderate tensile strength, making it suitable for applications where strength is needed but not at the expense of flexibility. Higher-strength films are better for bags and packaging that require durability.
- Elongation at Break: LDPE films have high elongation at break, meaning they can stretch significantly before they tear. This is particularly useful in applications like stretch film for packaging, where flexibility is essential.
The Film Extrusion Process with LDPE Granules
The extrusion process for LDPE film involves several key steps that transform the granules into a continuous, thin film:
- Melting and Mixing: LDPE granules are fed into an extruder, where they are melted by applying heat and pressure. The temperature is usually kept between 160°C and 220°C, depending on the exact formulation and desired film properties. The extruder’s screw design and temperature zones help ensure a homogenous melt, free from air bubbles or unmelted particles.
- Extrusion through a Die: The melted polymer is then forced through a die, which determines the thickness and width of the film. There are two common types of extrusion processes:
- Blown Film Extrusion: In this process, the molten LDPE exits the die as a thin tube and is then inflated to create a bubble, which is cooled and flattened into a film. Blown film extrusion is ideal for producing thin films with a good balance of strength and flexibility, and is commonly used for bags and packaging films.
- Cast Film Extrusion: In cast extrusion, the melt is extruded through a flat die onto a cooled roll, creating a flat film. This method is preferred for films requiring high clarity and uniform thickness, such as cling films and food wraps.
- Cooling and Solidification: In both extrusion methods, the molten film is rapidly cooled using air or water. Cooling is essential to prevent deformation and ensure the film solidifies quickly, resulting in a smooth, uniform surface.
- Winding and Finishing: The cooled film is then wound onto rolls for further processing, such as slitting, printing, or bag making. The film’s properties can be further modified with additives to enhance qualities like UV resistance, slip, or anti-fog properties.
Applications of LDPE granule for extrusion film
LDPE’s versatility makes it suitable for a wide range of applications, including:
- Packaging: LDPE films are used in food packaging, grocery bags, and shrink wraps. Their flexibility, transparency, and sealability make them ideal for wrapping fresh produce, frozen foods, and consumer goods.
- Agricultural Films: LDPE is commonly used in greenhouse covers, mulch films, and silage wraps. The film’s durability and resistance to moisture and chemicals protect crops and improve soil quality.
- Construction and Industrial Use: LDPE films serve as vapor barriers, protective covers, and liners in construction. They are lightweight, easy to handle, and provide an effective barrier against moisture and dust.
Modifying LDPE Films with Additives
LDPE granules can be mixed with additives to enhance or modify the film’s properties for specific applications:
- UV Stabilizers: Added to prevent degradation under sunlight, extending the lifespan of agricultural films.
- Slip Agents: Reduce friction, making the film easier to handle and preventing it from sticking to machinery during processing.
- Anti-Blocking Agents: Prevent the film layers from sticking together, which is essential for rolls and bags.
- Anti-Fogging Agents: Used in food packaging films to prevent condensation from forming inside the packaging.
Choosing the Right LDPE granule for extrusion film
When selecting LDPE granules for film extrusion, consider factors like desired film thickness, processing method, and final application requirements. Choosing the correct MFI, density, and any necessary additives will help you achieve optimal film quality and performance.
Typs of grade
1905U0:“1905U0” typically refers to a specific grade of Low-Density Polyethylene (LDPE) produced by various manufacturers. LDPE grades are generally identified by specific alphanumeric codes to denote distinct properties and applications. Let’s break down what this grade typically means in terms of its properties and uses.
1965N0:LDPE 1965N0 is another specific grade of Low-Density Polyethylene (LDPE), often designed for specialized applications like film extrusion.
2005EC:LDPE 2005EC is a specific grade of Low-Density Polyethylene (LDPE), typically used for film extrusion applications, especially for thin and flexible film production, like in packaging materials.
2015N0:LDPE 2015N0 is a specific grade of Low-Density Polyethylene (LDPE) that’s commonly used in film extrusion, particularly for applications requiring flexibility and durability, such as packaging films and agricultural films.
2100N0W:LDPE 2100N0W is a specific grade of Low-Density Polyethylene commonly used for film extrusion, designed for applications that require flexibility, strength, and good processability, such as industrial films, packaging, and liners.
2102N0W:LDPE 2102N0W is a grade of Low-Density Polyethylene (LDPE) often used in the production of films, especially in applications that require a balance between flexibility, durability, and ease of processing.
2102X0:LDPE 2102X0 is a specialized grade of Low-Density Polyethylene (LDPE) commonly used for applications requiring high clarity, flexibility, and durability, such as packaging films, liners, and other types of plastic films.
2200H0:LDPE 2200H0 is a specific grade of Low-Density Polyethylene (LDPE) commonly used in various applications, particularly in film extrusion processes. Below are the typical characteristics and applications of LDPE grade 2200H0.
2201H0:LDPE 2201H0 is another specific grade of Low-Density Polyethylene (LDPE) that is commonly used in film extrusion and various packaging applications.
2201H1:LDPE 2201H1 is a specific grade of Low-Density Polyethylene (LDPE) often used in film extrusion and various packaging applications. This grade is designed to offer a balance of flexibility, durability, and processability. Below are the typical characteristics and potential applications of LDPE grade 2201H1.
2201H3W:LDPE 2201H3W is a specific grade of Low-Density Polyethylene (LDPE) that is typically utilized in various applications, particularly in film extrusion processes.
2202H3W:LDPE 2202H3W is a specific grade of Low-Density Polyethylene (LDPE) that is commonly used in various applications, particularly in film extrusion processes.
2308N0:LDPE 2308N0 is a specific grade of Low-Density Polyethylene (LDPE) often utilized in film extrusion and various packaging applications
2402H0:LDPE 2402H0 is a specific grade of Low-Density Polyethylene (LDPE) that is used in various applications, particularly in film extrusion processes.
2404EC:LDPE 2404EC is a specific grade of Low-Density Polyethylene (LDPE) that is often utilized in film extrusion and other applications requiring flexibility, durability, and good processability.
2404N0:LDPE 2404N0 is a specific grade of Low-Density Polyethylene (LDPE) that is commonly used in film extrusion and various other applications that require flexibility, durability, and good processing characteristics.
2501N0:LDPE 2501N0 is a specific grade of Low-Density Polyethylene (LDPE) commonly used in various applications, particularly in film extrusion and packaging.
2601X1:LDPE 2601X1 is a specific grade of Low-Density Polyethylene (LDPE) that is commonly used in various applications, particularly in film extrusion and packaging.
2602X1:LDPE 2602X1 is a specific grade of Low-Density Polyethylene (LDPE) that is often utilized in various applications, particularly in film extrusion and flexible packaging.
7019EC:LDPE 7019EC is a specialized grade of Low-Density Polyethylene (LDPE), often formulated for specific applications such as film extrusion where high strength, clarity, and flexibility are required.
HP0321NN:HP0321NN is a grade of High-Density Polyethylene (HDPE), commonly used in applications that require high stiffness, impact resistance, and durability. This specific grade is often utilized in injection molding and blow molding processes, ideal for producing rigid products and containers.
HP0322NN:HP0322NN is a grade of High-Density Polyethylene (HDPE), designed primarily for applications that require high stiffness, impact resistance, and excellent durability. This grade is widely used in injection molding and blow molding processes, particularly for making rigid products and containers, such as industrial parts and storage solutions.
HP0722NDF:HP0722NDF is a specialized grade of High-Density Polyethylene (HDPE), commonly used in applications that require both high rigidity and enhanced processability. This grade is typically designed for film extrusion applications, which are often seen in packaging materials, liners, and various industrial films.
HP0723JN:HP0723JN is a grade of High-Density Polyethylene (HDPE) commonly used in blow molding applications due to its high stiffness, good impact resistance, and ease of processing. This specific grade is often suitable for producing containers, bottles, and other molded items that require strength and durability.
HP0823JN:HP0823JN is a High-Density Polyethylene (HDPE) grade commonly used in blow molding applications. It’s designed for applications that require high strength, rigidity, and impact resistance, making it ideal for producing containers, bottles, and various rigid packaging solutions.
HP0824NDF:HP0824NDF is a High-Density Polyethylene (HDPE) grade specifically formulated for film extrusion applications. This grade is often used in products requiring high stiffness, excellent processability, and durability, such as industrial films, heavy-duty packaging, and liners.
HP20023:HP20023 is a High-Density Polyethylene (HDPE) grade commonly used in pipe extrusion and pressure pipe applications due to its high strength, excellent resistance to environmental stress cracking, and durability. This grade is ideal for applications requiring rigidity, impact resistance, and long-term performance, such as water pipes and gas pipelines.
COMPOUND LDPE granule for extrusion film
Compound LDPE Granules are modified Low-Density Polyethylene (LDPE) granules specifically formulated for extrusion film applications. These compounds are LDPE-based materials enhanced with additives or blended with other polymers to tailor their properties for specific requirements, such as improved strength, flexibility, transparency, and processability.
recycled granule for packaging
Recycled Granules for Packaging are polymer granules derived from post-consumer or post-industrial plastic waste, processed and refined to be reused in various packaging applications. These granules, typically made from recycled LDPE, HDPE, or polypropylene (PP), are an eco-friendly alternative that helps reduce plastic waste and conserve resources, often utilized in making films, bags, containers, and non-food packaging materials.
compound granule for ships and airplanes
Compound Granules for Ships and Airplanes are specially formulated polymer granules designed for use in the manufacturing of components and parts for the aerospace and marine industries. These compounds are tailored to meet the stringent performance requirements and regulations specific to these sectors, which include lightweight materials, high strength, durability, and resistance to environmental factors.
compound granule for plastic bag
Compound Granules for Plastic Bags are specially formulated polymer granules designed for the production of plastic bags. These granules are often made from blends of polymers like Low-Density Polyethylene (LDPE), Linear Low-Density Polyethylene (LLDPE), or High-Density Polyethylene (HDPE), along with various additives to enhance their properties for specific applications.
wholesaler
Finding a wholesaler for compound granules suitable for plastic bags involves several considerations, including the type of plastic required, volume needs, pricing, and geographic location.
trader
When looking for traders or wholesalers for compound granules used in the production of plastic bags, there are several avenues to explore. Traders often act as intermediaries, helping you source the required materials from manufacturers or suppliers.
supplier
When searching for suppliers of compound granules for plastic bags, it’s important to consider both local and international options that offer the specific types of materials you need.
FQA About LDPE granule for extrusion film
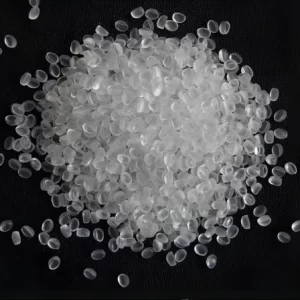
What is LDPE, and why is it commonly used for film extrusion?
LDPE (Low-Density Polyethylene) is a thermoplastic known for its flexibility, strength, and transparency. It has a low melting point and high elasticity, making it easy to process for film extrusion and ideal for applications like packaging, agricultural films, and consumer products that require a balance of durability and flexibility.
Is LDPE film recyclable?
Yes, LDPE film is recyclable. It’s typically assigned the recycling code #4, and it can be reprocessed into new products, although recycling facilities may vary by location.
What are the typical properties of LDPE used in film extrusion?
LDPE for film extrusion has:
- Density: 0.910 – 0.940 g/cm³, giving it flexibility and transparency.
- MFI: 0.2 to 20 g/10 min, which controls flow and thickness.
- Tensile Strength: Moderate, for balanced strength and flexibility.
- Elongation at Break: High, allowing the film to stretch without breaking.
What is the Melt Flow Index (MFI), and why is it important?
The Melt Flow Index (MFI) measures how easily the polymer flows when melted. It’s crucial because it affects the thickness and strength of the film:
- Lower MFI: Suitable for thicker, more durable films.
- Higher MFI: Best for thinner films with better flow, often used in lightweight packaging.